Plate heat exchangers
Innovative Plate Technology
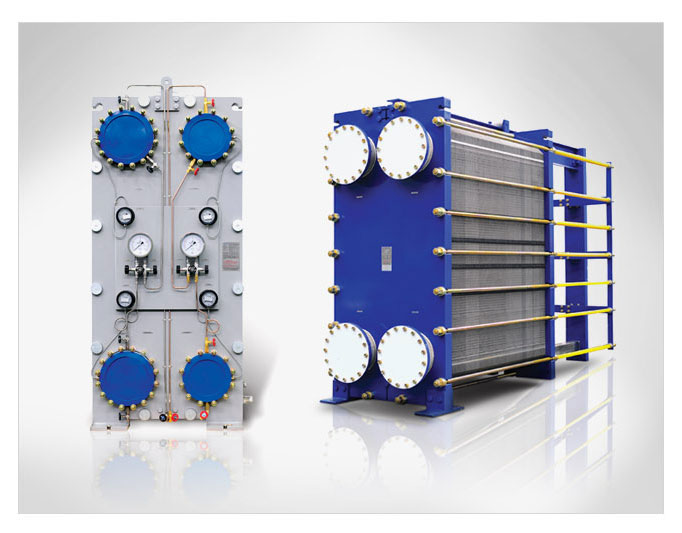
Principle
Plate heat exchangers have more than 100 years history and its structure is composed of a fixed frame, a movable frame and corrugated plates which are in between the two frames.
Hot liquid and cold liquid go through between the corrugated plates in turn.
To prevent leaking, gaskets are mounted around the plates and tightening bolts are used to put the plates together.
There is heat transfer between the two liquids through the plates.
This is the main principle of a plate heat exchanger.
The arrangement of two liquids is that the cold liquid goes upward and hot liquid goes downwards in order to increase heat transfer efficiency.
There is an advantage to use plate type heat exchangers over Shell & Tube type heat exchangers, that is to say, the corrugations in the plates increases the liquid turbulence to a low Reynolds number and the liquids flow is counter current so that the heat transfer efficiency is always 3 ~ 5 times higher than Shell & Tube type heat exchangers.
Features
(1) High Heat Transfer Coefficients
DHP Plate Heat Exchangers provide high rates of heat transfer, due to the turbulence inducing shape of the plates.
The special gasket configuration of the plates prevents any mixing of the media being processed.
In the port area both fluids are separated by double gaskets.
Additional safety is ensured by the leakage gap.
(2) Saving the installation space
Since the heat transfer efficiency is high, only 2-30% installation space is required comparing to the same capacity of the multi-tubular heat exchanger.
(3) Low contamination
Strong turbulent flow formed by the bump in flow way and short staying time of the fluid inside the heat exchanger will result in getting the effect to avoid scale adhesion. Convenient disassembling and assembling. Cleaning is easy to handle the contamination in an efficient way.
(4) Minimum heat loss
Heat is emitted in the side of the plate type heat exchanger and because the space is not much required the heat loss can be minimized due to less heat generation volume even when insulation or heat insulating materials are not used.
(5) Applicability & standardization
All the components or parts are standardized and the compatibility of the parts is good. Plate number can be increased or decreased depending on the change of the capacity. Cleaning or replacement is easy when the plate or gasket is worn out.
Specification
Max. Operating Temperature | 190℃ |
---|---|
Max. Operating Pressure | 20kg/㎠ (for high pressure 50kg/㎠) |
Plate Material | STS304, 304L, 316, 316L, 317, AVESTA, 254SMO, HASTELLOY-B, C, Titanium, Ti-Pd, NLCP(Nickel), AL-BRASS |
Gasket Material | Nitrile(NBR), HNBR, HYPALON, BUTYL, FPM, FPM-G EPDM(Ethylene Propylene Diene Methylene), Silicone Neoprene |
Frame Material | Carbon Steel, STS304, 316 |
Applications
Foods | Milk, juice, sugar solution, soy and sesame oil, liquor, beer, heating, sterilization/cooling for edible oil, etc., heat recovery, and CI P liquid heating |
---|---|
Chemical | Petroleum, paraffin, various acids, sulfuric acid, kerosene, salt sulfate, zinc, nucleic acid, polymerization process, soft water cooling, heating for glycerine, etc., condensing ethanol, etc. |
Textile | Washing water, NaOH solution, dyeing water cooling and waste heat recovery |
Electric & electronic | Circulating water, flushing coolant, transmission oil cooling, rectifier transformer, SCR cooling, high frequency heat treatment cooling, pure water treatment, electron tube cooling and blackening furnace cooling |
Mechanical facility | Machineries cooling, emulsion, hydraulic oil, abrasive liquids cooling, compressor, industrial furnace cooling, transmission oil, autoclave water cooling and engine cooling |
Ship-building | Central Cooling, Lub Oil, Jaket, Piston Water, Heavy Oil, Transmission Oil cooling, Diesel Oil, Heating Oil preheating |
Steel Iron | Mould cooling, cooling for continuous casting process, furnace, coking plant cooling, emulsion, ammonia water cooling, machineries, compressor cooling, washing oil cooling, hydraulic oil cooling, heat recovery for washing water and other waste heat recovery processing |
Surface treatment | Sulfate cooling, phosphate, heating/cooling for pretreatment process liquid of coating, heat treatment liquid cooling, galvanizing and chrome coating |
Extraction process | Crude Alcohol, Soy Bean Oil, Cooling for fatty acid, etc. and heating for coconut oil, edible oil, etc. |
Pharmacy | Cooling, heating and concentrating for extracting solutions, cream, sugar solution, emulsion, suspension, plasma, citric acid, etc. |
Paper pulp | Washing water, chlorine water cooling and waste heat recovery |
Building equipments | Heating, heating for hot water supply, heating and cooling for HVAC, etc., condenser, evaporator, heat pump cooling, hydraulic oil cooling and waste heat recovery |
Automobile | Cooling for heat treatment solution and cutting fluid, heating for pretreatment of coating and paint cooling for spray booth (Phosphatizing sol. cooling) |
Fish tank | Fish tank sea water heating, waste heat recovery, incubator and fish farm |
Plant | Ice thermal storage system, district heating plant, nuclear power plant and swimming pool |